When Sorrel presented me the concept of crafting a green range firing the works once (no bisque), using recycled clay, and reclaimed mystery glaze. I was somewhat hesitant at first given all the reasons why we bisque in the first place, to avoid weak walls, pin holing, bloating, cracking etc not to mention an untested mystery glaze... But as they say, "nothing ventured, nothing gained". So I went to work and recycled 10kg's of clay and began throwing with the sort of optimism one might expect from a fresh project.
Ten cups later and a few random bottles, I poured off the water from the mystery glaze. Everything was prepared, the cups were made from for-mentioned reclaimed clay, pieces were looking fabulously trimmed and the mystery glaze was primmed for application.
We decided to stick with using our liner glaze on the interior of the cups and reserving the mystery glaze for the exterior. The balance of the mystery glaze could have shifted due to it being collected from cleaning glaze brushes and containers. Sorrel substituted kaolin for ball clay in our clear glaze recipe upon reading it from somewhere (reason pending).
So Let's begin:
I set aside four cups to dry out further before glazing and began to glaze the first 4 at leather hard stage. I decided to pour the insides first with our usual clear gloss glaze and then another cup with the substituted ball clay. On pouring, the only noticeable difference at this point was the silky look of the kaolin in comparison to the ball clay recipe (maybe the kaolin retains more moisture causing a wetter wall) - a thought that occurred to me as I type this account.
As expected, both cups became instantly soft. I placed them on top of the kiln to dry out while I got to work on the others.
Experimenting further, I tested another two more cups by fully immersing them (these had dried out a little more than the leather hard pieces). I didn't hold out a lot of hope for this method, but I couldn't resist the urge to dip! I surrendered to the allure of the bucket of creamy white and dunked it quickly... Results indicated: The first cup began to reveal a few wall welts here and there and the second, slightly drier, fared better with no wall welts at all.
Once all pieces had sufficient drying time (walls still had some moisture), I then proceeded to experiment with pouring and painting on the mystery glaze. Pouring, whilst fun, proved to be a riskier option than paint on method. The glaze pooled in the recesses under the pot, quickly softening the wall, one also needs to wipe the base completely before sitting it down. I almost lost a foot to one of my cups as the glaze turned the foot to slip. Paint on method was much more controlled, but application was thin, when applying a thicker brush load the walls softened quickly. Using a random brushstroke style, with more abstract markings seemed to suit this process. I am yet to try spraying and will do on my next round of eco pot experiments.
With the kiln loaded for tomorrow's firing, the culmination of today's efforts remains a mystery until Friday's reveal. Reflecting on my journey thus far -
Through glazing on greenware the process revealed new methods of application. I felt myself being propelled towards uncharted paths and infusing the process (and me) with a sense of vitality.
Tune back in for the big reveal on Friday to see the outcomes of the once fired pots.
EDIT
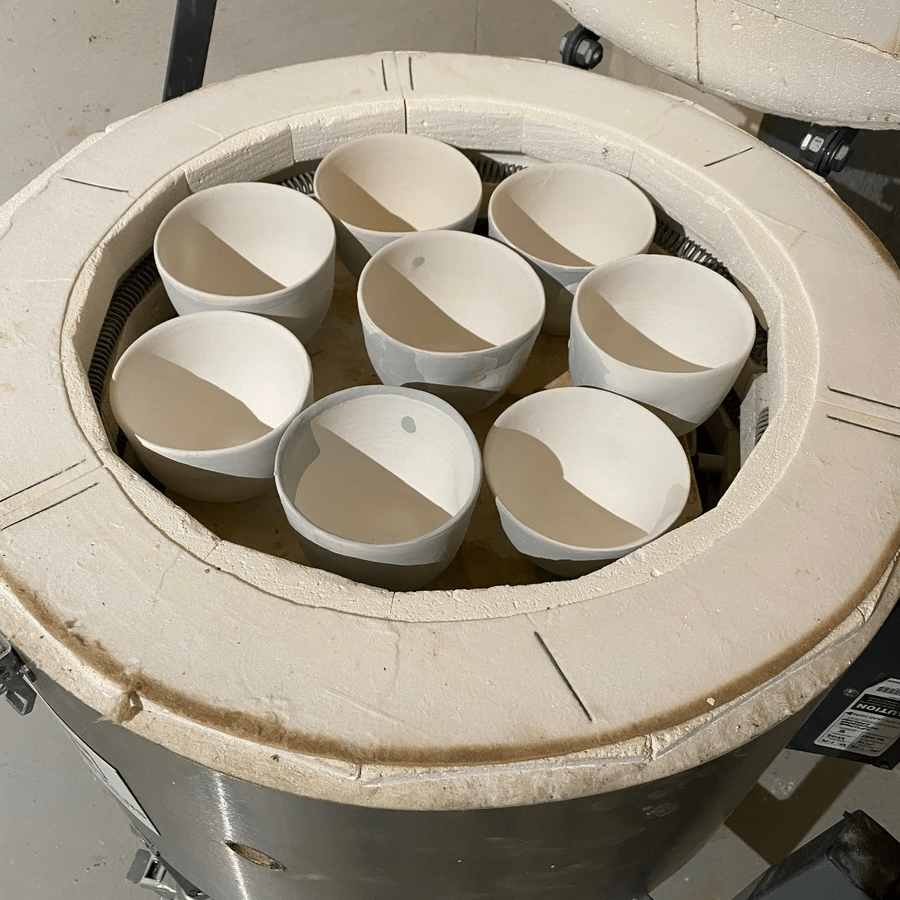